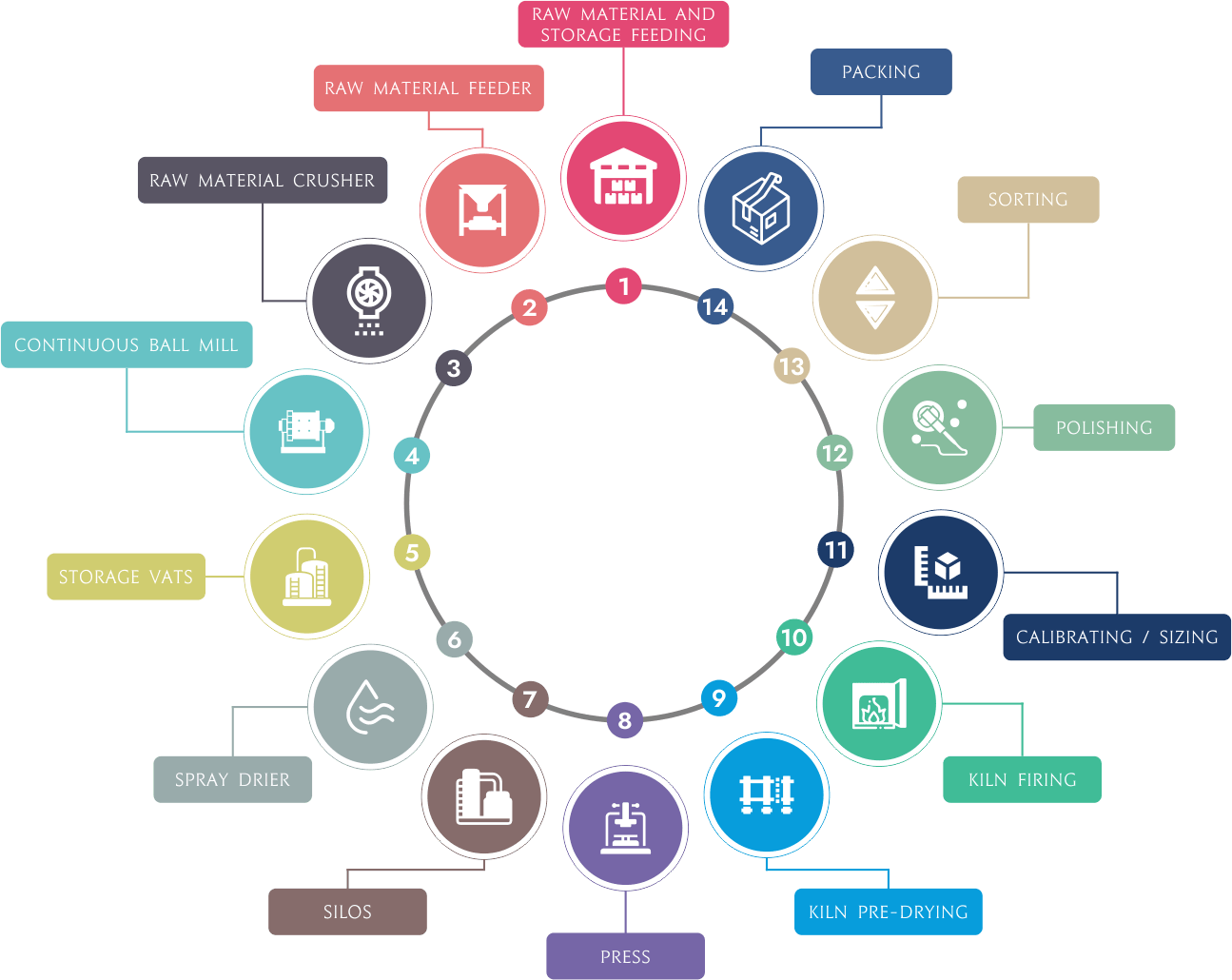
01
Raw Material and Storage Feeding
The major raw materials used in the manufacturing of Vitrified Porcelain Tiles are Ball Clays,Soda Feldspar, Potash Feldspar, Quartz, China Clay, Talc, Zirconium Silicate and body stains.
02
Raw Material Feeder
These raw materials are stored in individual locations, and are taken out from theirrespective locations for loading into a box feeder, with a weighing belt to facilitate weighing different materials before feeding into the balls mills via conveying system.
03
Raw Material Crusher
The raw material from the feeder is conveyed to the crusher, to bring the particle to the required mesh size, suitable for ball mill grinding.
04
Continuous Ball Mill
The raw materials are then ground in ball mills to make homogeneous slurry and to reduce the particle size of the raw materials. Alumina pebbles are used as a grinding media. The water input in the ball mill is controlled by an automatic water flow meter to achieve the correct density of slip.
05
Storage Vats
After grinding, the slip is discharged into storage tanks called Vats. The slip is then agitated continuously with high efficiency stirring blades to ensure homogeneity.
06
Spray Drier
In this process, the slip from storage vats is sieved and is fed into the spray drier at a constant pressure by means of a high-pressure piston pump. In the spray drier the slip is atomized against hot air to convert slip into granules.
07
Silos
The spray dried granules are stored in silos. Ageing of granules in silos increases the working properties of the granules by homogenizing the moisture.
08
Press
The granules are then pressed under high pressure by means of an automatic hydraulic press to facilitate formation of tiles of different sizes.
09
Kiln Pre-Drying
After pressing, the tiles are moved into a horizontal dryer, where the moisture content in the tile evaporates and the tile picks up its mechanical properties (strength).
10
Kiln Firing
Firing is an extremely important stage in the production process since vitrification takes place in this stage. The peak temperature is approximately 1250 oC. The flux in the body melts and resolidifies to form porcelain stoneware. The vitrification process enables the tile to have various mechanical and chemical properties. As firing progresses and temperature increases, the material passes through a number of critical thermal zones, including the cooling at the very end of the kiln.
11
Calibrating / Sizing
Fired tiles are fed to the first calibrating unit by a conveyor. Calibration is done to make the surface even by removing a certain amount of material to provide a flat surface. Diamond tools are employed for calibration.
12
Polishing
Polishing employs tangential heads to give the tile a mirror like finish without any scratches, shadows or signs of machining. This stage also ensures the squaring and chamfering of sides.
13
Sorting
With the help of the latest technology, the tiles are automatically sorted into different grades depending on the categorization. The tiles are checked for dimensions, flatness automatically and sorted into appropriate grades.
14
Packing
The categorized tiles are packed in corrugated boxes by an automatic packaging unit, and ready for dispatch. Quick Link fenix ceramic fenix ceramic fenix ceramic fenix ceramic